The goal was to design a system for the automation of tobacco flavor mixing that would ensure maximum accuracy when combining various ingredients. The customer required the process to be fully automated and to guarantee consistent quality of the final product. The main challenge was the precise control of the mixing process because different ingredients vary in viscosity, which could affect the flow and thus the accuracy of the final mixture.
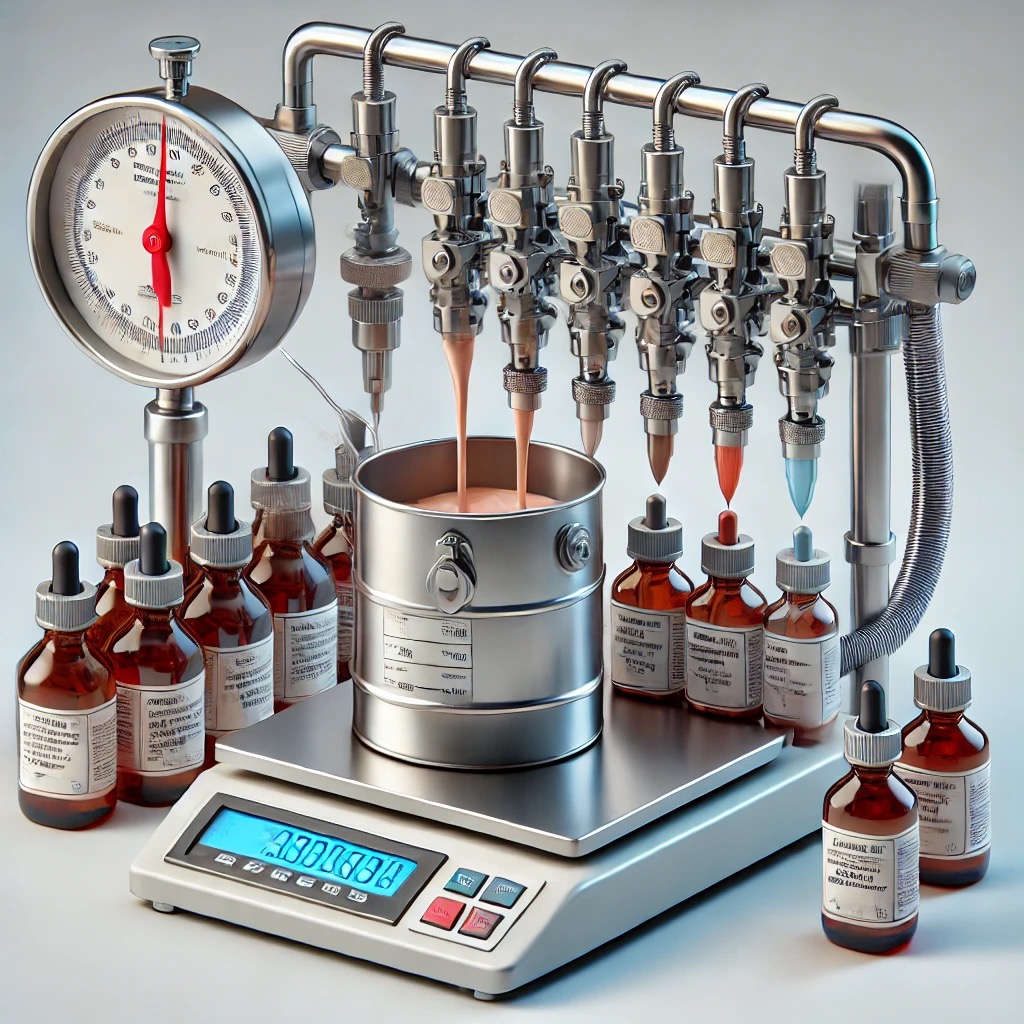
The solution involved using a Raspberry Pi connected to scales and pumps, which formed the core of the system. The Raspberry Pi was equipped with a web server that allowed for remote control and monitoring of the process.
The pumps could precisely control the speed and direction of flow based on data from the scales, ensuring the correct dosing of each ingredient in the mixture. The system was designed to automatically slow down the flow toward the end of mixing, increasing the accuracy of dosing. For safety, a physical emergency stop button was added. To connect the pumps to each other, we used MODBUS and a daisy chain configuration of the pumps (one cable running from pump to pump).